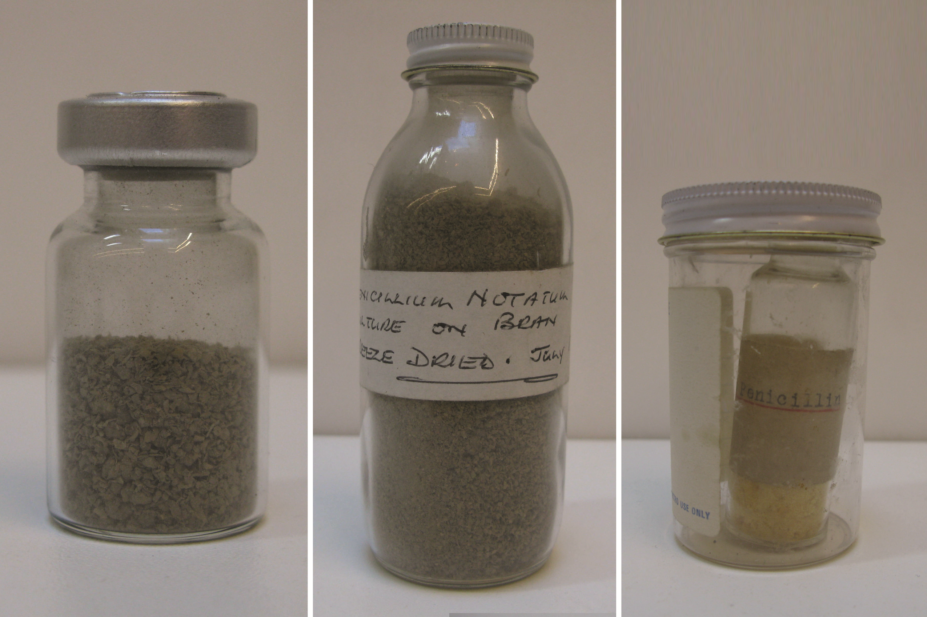
RPS Museum
I and a few other newly qualified pharmacists joined the Allen and Hanburys factory in Ware, Hertfordshire, in August 1944. The company was licensed by the government to produce benzyl penicillin, which was urgently required by the medical services of the armed forces.
Glass milk bottles were used to grow the penicillin cultures. The Pyrex glass containers that professors Florey and Chain had used at Oxford University to make the first clinically used penicillin were expensive to produce, and their production facilities were required to make other essential war materials. Pint bottles were comparatively easy to make, and were needed for milk bottling and for the beer trade. We worked in a pilot plant, intended to provide the experience to operate a larger production unit that was still being constructed and fitted out. The pilot plant contained an incubator room set at 22°C. There was also a bottle-washing machine, a nutrient media making plant, bottle filling equipment — which filled the correct quantity of nutrient broth into the bottles — and an autoclave to sterilise the filled bottles. A small aseptic room, close to the autoclave, was where the cooled sterilised bottles and their contents were inoculated with the fungal spores.
The mould inoculum was grown on sterilised moist bran, and blown into bottles filled with sterilised nutrient broth. The bottles were placed on their sides to maximise the surface area for the mould to grow, and hence to maximise the yield of penicillin. The bottles were laid on racks and wheeled into the incubator room. The incubation time was from seven to eight days, when the maximum yield was achieved.
Source: Courtesy of Richard Felix
Richard Felix FRPharmS was one of a team of pharmacists tasked with producing penicillin at a small wartime manufacturing plant
Probably a thousand bottles were filled and emptied daily, mostly by hand.
The bottles were emptied through a sieve-like unit to extract the penicillin. The mould was retained on the sieve and the clear broth containing the penicillin fell by gravity on to a bed of charcoal. The penicillin was adsorbed onto the charcoal. Butyl alcohol was used to wash the penicillin out of the charcoal, and aqueous sodium or calcium and chloroform were used to precipitate outsodium or calcium benzyl penicillin salts.
Neither protective clothing nor masks were used at the time, and the operators often succumbed to the anaesthetic effect of the chloroform.
The cleaned-up sodium or calcium salts were freeze-dried. The resulting product was very impure: it was yellow in colour, and had of a potency of about 200 units per milligram, compared with the output from Glaxo Laboratories and the Distillers Company which was white in colour with a potency of about 1400 units per milligram.
The availability of benzyl penicillin was a challenge to the formulating pharmacist tasked with producing end-products containing it. To give some idea of this work, an oily suspension for injection was made, and lozenges for sore throats were also produced — although these had an adverse effect on the bacterial flora of the mouth. An ointment form was also developed. A chewing gum was also studied, but it failed because of the difficulty in making the gum base into a suitable formula. These and other forms had very short commercial lives because of side effects, and the need to use penicillin for life-threatening illnesses.
By late 1944 to early 1945, both Glaxo and the Distillers Company began producing penicillin by the deep fermentation method in 5,000–10,000 gallon stainless steel tanks. This method produced higher yields of better quality product and was more economical than the bottle method. The Allen and Hanburys contract was cancelled in the autumn of 1945 by Harold Wilson who was then president of the Board of Trade.
As a result, there were thousands of bottles parked on site which were never used. They were sold to a vinegar bottler in the east-end of London, I presume at a good price!
You may also be interested in
Long service of members
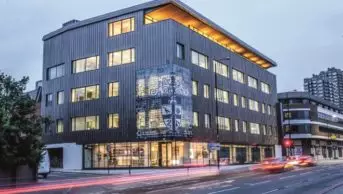
Membership fees 2022
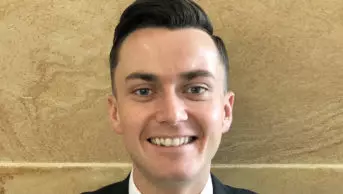